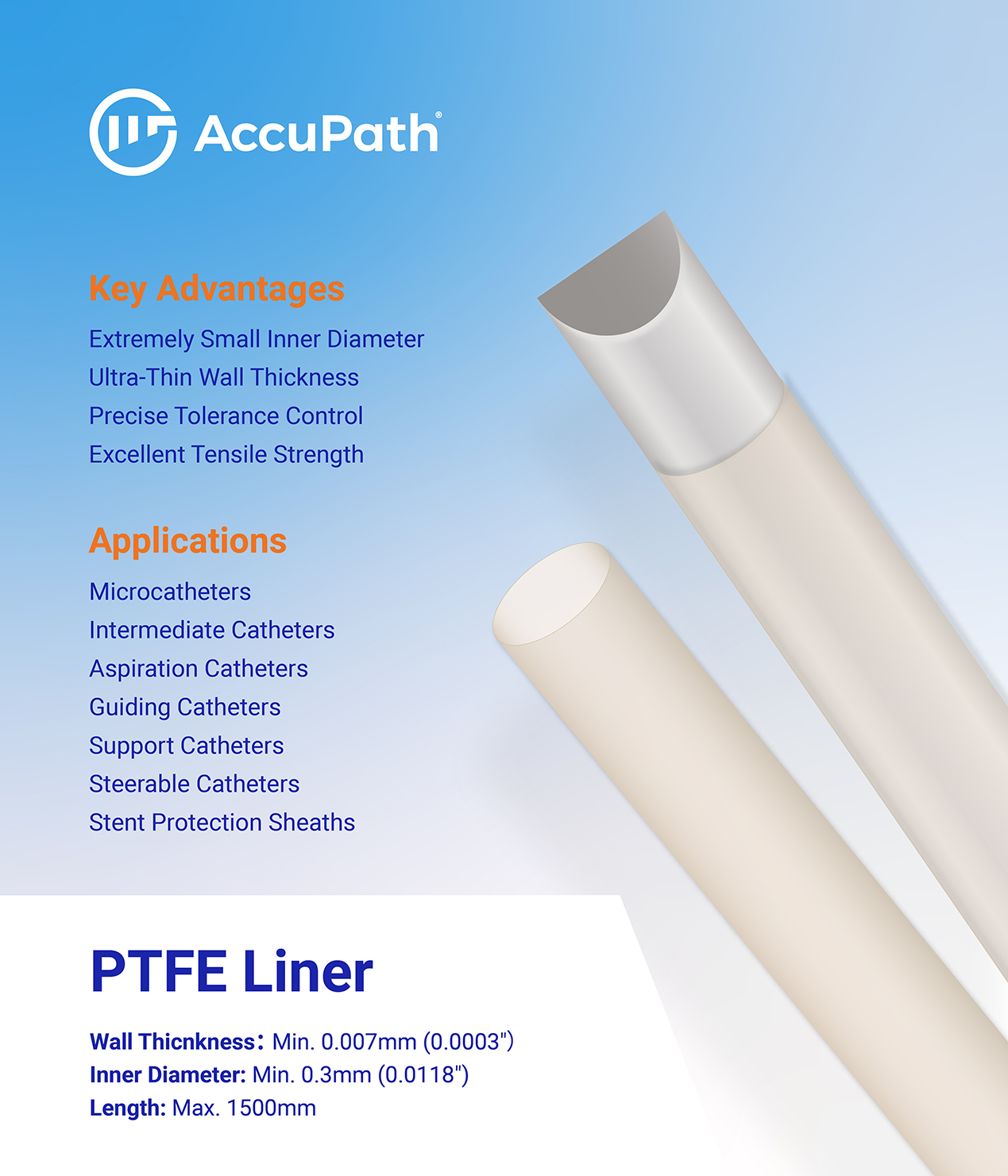
Abstract
PTFE Liner, characterized by their excellent lubricity, thin walls, strong flexibility, and high tensile strength, are becoming the core material for vascular interventional catheters. AccuPath® boasts advanced dipping, free extrusion, and mandrel extrusion processes, which elevate the performance of PTFE Liner to new heights, providing infinite possibilities for the design and application of interventional catheters. Thanks to a rigorous quality control system, the stability of AccuPath® products has also been unanimously recognized by customers.
Compared to vascular interventional catheters of the past, modern catheter products are designed with increasing precision, composed of intricate components such as lining tubes, adhesive layers, braided layers, and outer materials. Achieving thinner catheter walls and larger internal diameters is a continuous goal for manufacturers of interventional catheters. PTFE Liner, with their excellent lubricity, thin walls, strong flexibility, and high tensile strength, are widely used in medical devices such as microcatheters, intermediate catheters, aspiration catheters, guiding catheters, support catheters, steerable catheters, and stent protection sheaths.
However, striking a balance between dimensions, flexibility, and strength in PTFE Liner is a significant challenge in the product development and processing stages. This includes the complexities of forming intricate structures, material processing, multi-step process management, precise control over extrusion techniques, and the selection of molding methods.
AccuPath® is committed to the research and development of a range of high-performance PTFE Liner through continuous technological innovation and process optimization, to meet the growing demand for high-performance catheters in the medical industry.
1.Dip Coating (Film Casting) Process: A concentrated PTFE dispersion is evenly applied onto a metal mandrel, followed by sintering and curing to form a uniform coating. The metal mandrel is then progressively removed, resulting in PTFE Liner with outstanding flexibility.
2.Free Extrusion Process: After mixing PTFE powder with an organic solvent and lubricant to form a preform, an extrusion mechanism is shaped into a tubular form, which is then sintered. This process results in tubing with thin and even walls, with an optimized grain structure, thereby providing the tubing with greater axial strength and rigidity.
3.Mandrel-Assisted Extrusion Process: Combining the advantages of film casting, this process utilizes a mandrel to assist in the extrusion molding, ensuring the uniformity and flexibility of the lining tube walls, while significantly enhancing its strength. Additionally, by eliminating the step of reinserting the mandrel, this process maintains the adhesion properties on the surface of the tubing, making it suitable for continuous braiding processes and greatly improving production efficiency.
Product Performance under Different Manufacturing Processes
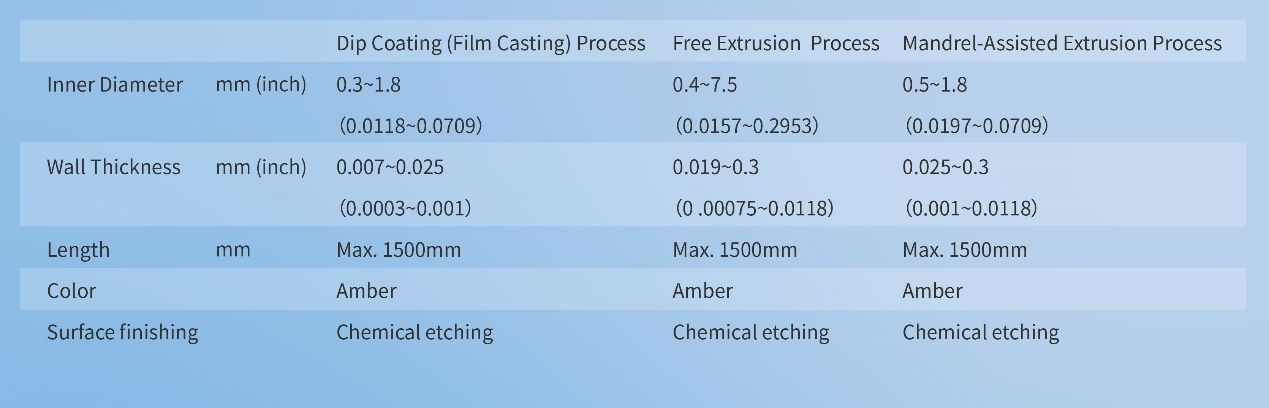
Data testing indicates that AccuPath® has elevated the performance of PTFE Liner to new heights, with product performance meeting or exceeding the mainstream market standards.
Ultra-Thin Wall Thickness and Uniformity
The PTFE Liner produced by the free extrusion process can achieve a minimum wall thickness of 0.00075 inches (approximately 19 micrometers), enhancing flexibility and transparency while reducing the diameter of the catheter, thus minimizing tissue damage.
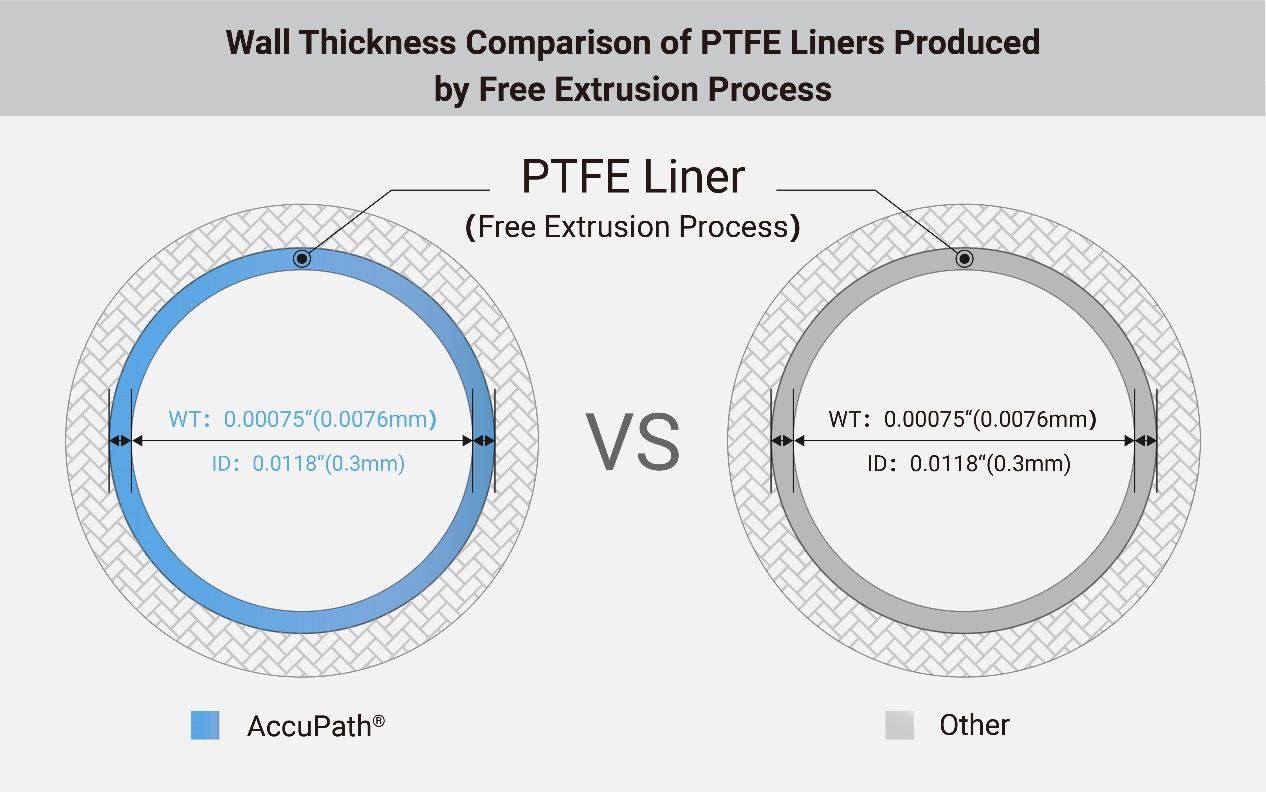
Outstanding Tensile Strength
While maintaining a smooth, delicate, and thin-walled profile, AccuPath® PTFE-lined tubes also exhibit high tensile strength, thereby enhancing durability.
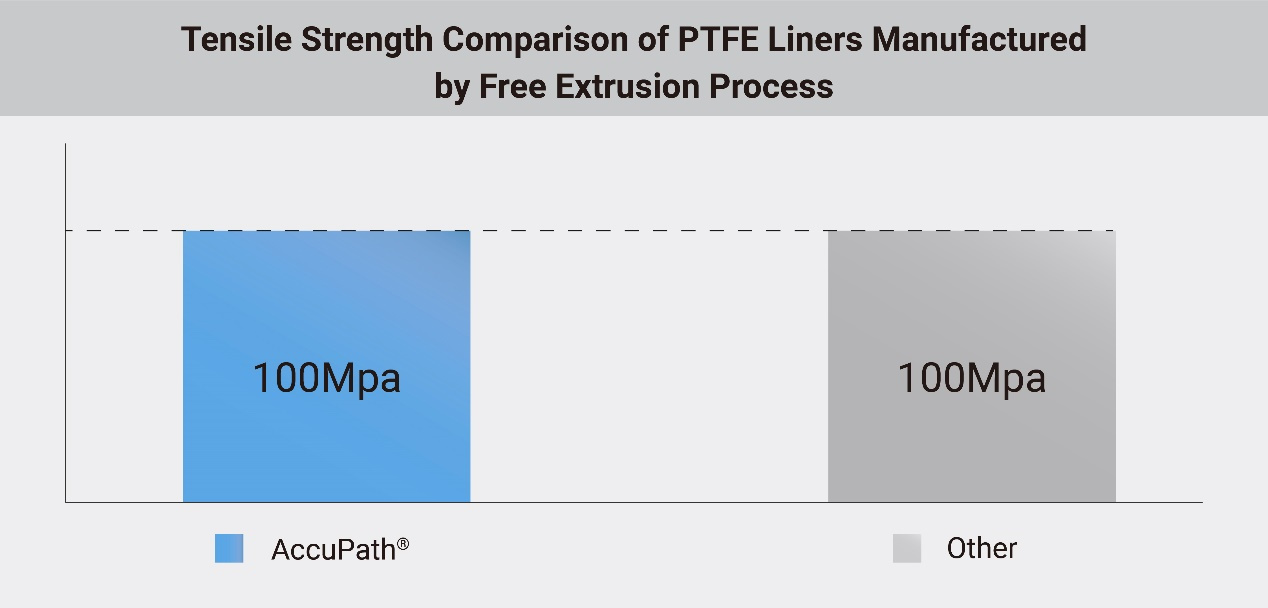
Precision Tolerance Control
By employing a mandrel-assisted extrusion technique with a silver-plated copper wire mandrel, we have achieved strict control over the internal diameter and wall thickness tolerances, providing reliable support for interventional catheters.
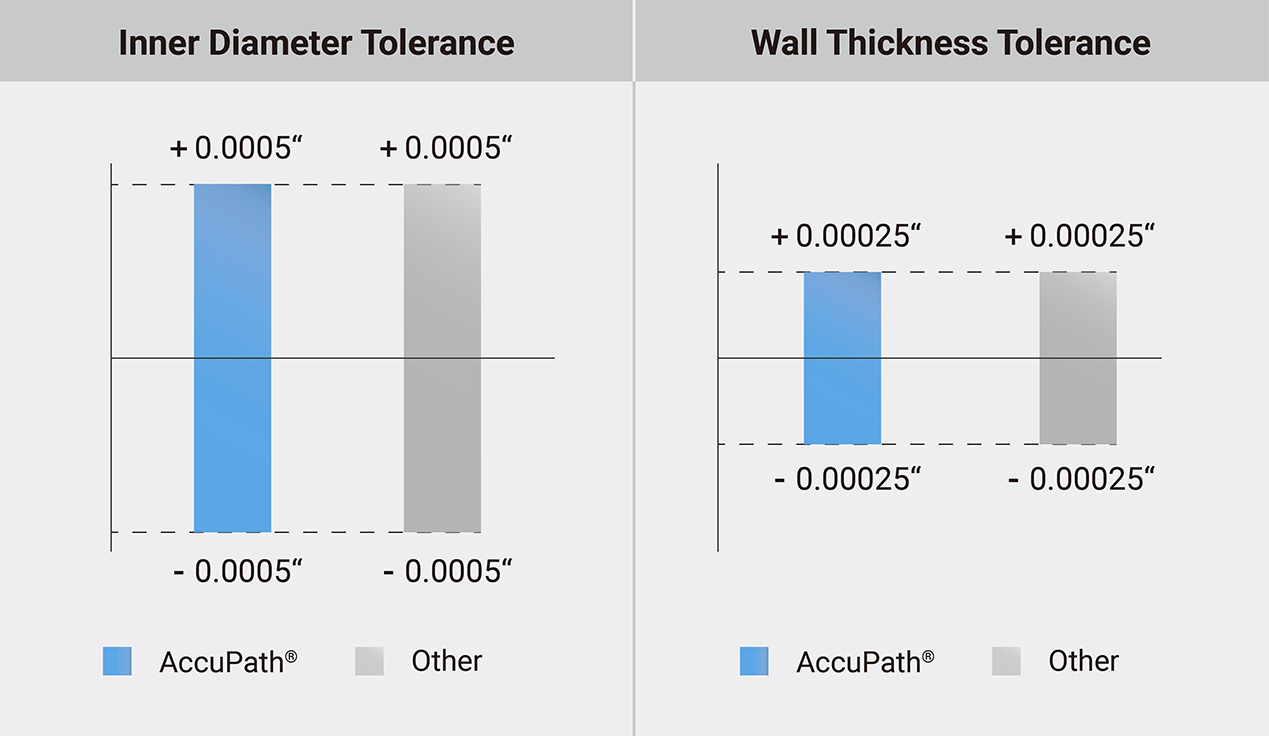
AccShrink® PET Heat Shrink Tubing Specification Matrix
Quality control
In terms of quality management, AccuPath® strictly implements the ISO 13485 quality system standards. This ensures that our products meet the biological requirements for medical devices. At the same time, we are equipped with advanced manufacturing equipment and precise measuring instruments, coupled with stringent inspection and testing methods to guarantee that product quality meets the usage requirements for medical devices.
Delivery Cycle
AccuPath® leads globally in terms of delivery cycles, with standard products available for delivery within two weeks and customized sizes deliverable within four weeks.
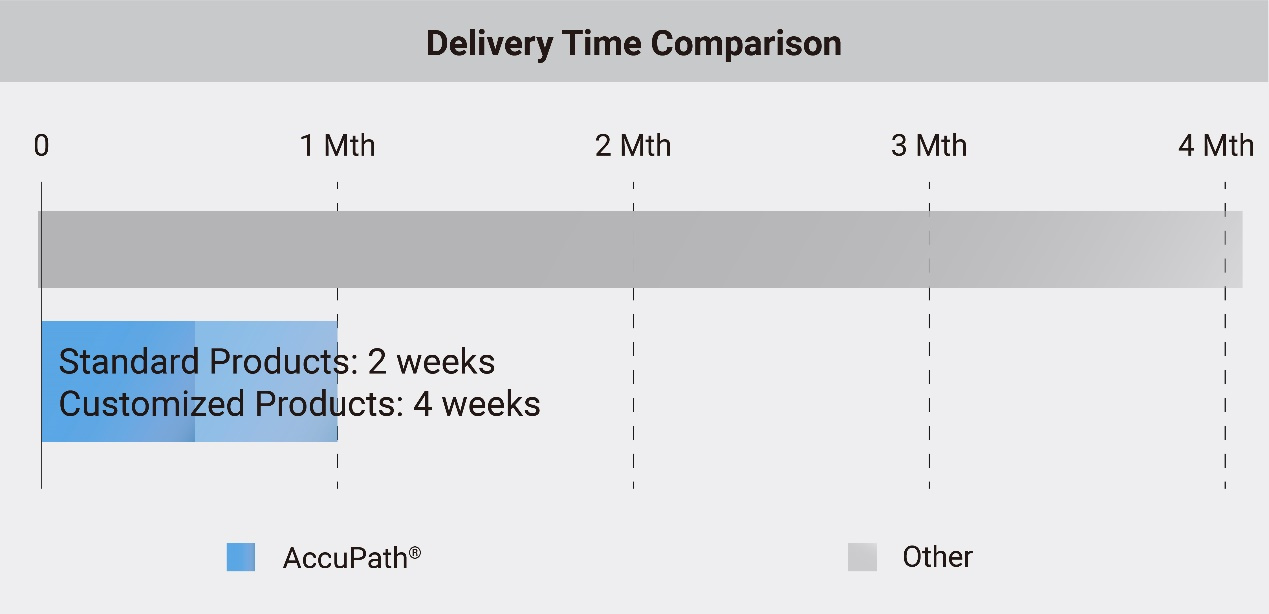
Post time: May-13-2024