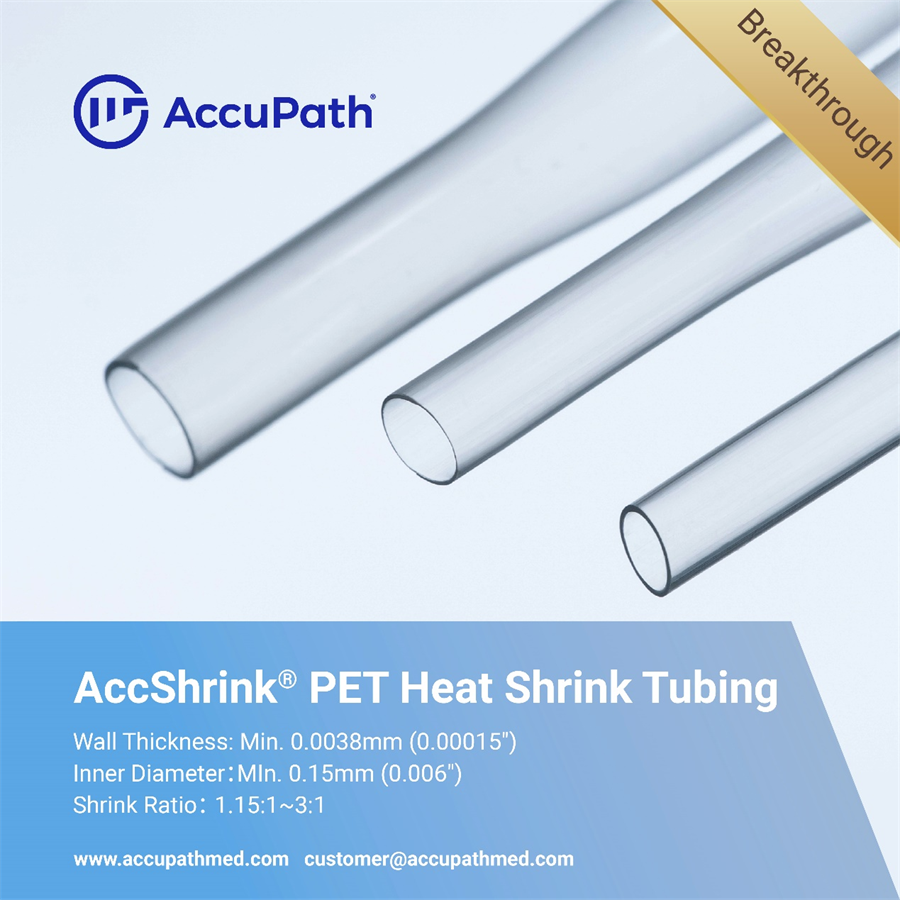
Abstract
In the field of medical devices, even minor improvements in product performance can lead to significant enhancements in therapeutic effects. However, medical device manufacturers inevitably face challenges in material selection and process precision when pursuing more refined and reliable products. AccuPath® offers high-quality products through innovative technology, effectively assisting clients in confidently addressing material and process-related challenges.
This article will use the example of PET heat shrink tubing technology to address the production and manufacturing pain points of the spring coil system, demonstrating how AccuPath® fully meets the manufacturers' demand for high-performance medical devices through precise process control, strict quality management, and customizable specification parameters, while achieving cost reduction and efficient delivery.
Typical case
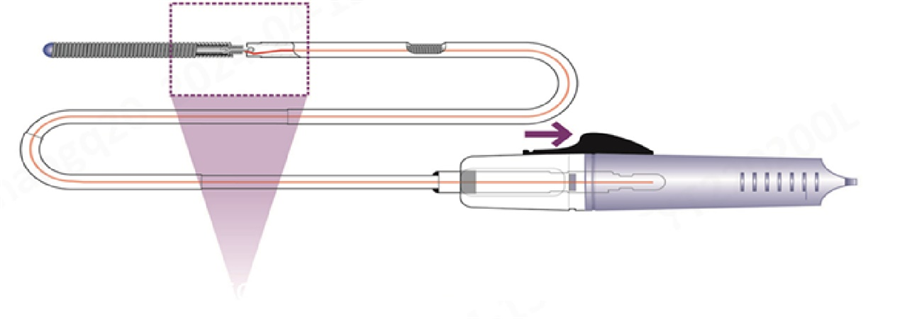
Spring coil structure display (graph source network)
Coil systems are typically composed of coils and a delivery system, which are clinically used to embolize aneurysms, arteriovenous malformations, and arteriovenous fistulas in intracranial and peripheral vessels. Different types of coils may have different intended purposes. The implantable part of the coil system generally includes: the coil wire body, an anti-unspooling structure, a hydrophilic core (if applicable), and microfibrils (if applicable); the delivery system part generally includes: a hub connector, an introduction sheath, a push rod (with radiopaque marker), the connection area with the coil (detachment zone), and auxiliary components (if applicable), etc.
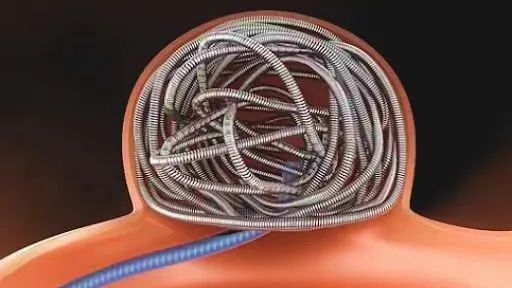
Clinical treatment 3D simulation diagram (graph source network)
The push rod accurately delivers the coil in clinical treatment, thereby achieving the therapeutic purpose of effectively sealing off the vascular tumor with the coil and preventing hemorrhage. During the clinical application process, the performance requirements for the push rod by the operator include: 1) 1:1 tactile feedback; 2) Smooth tracking ability and effective pushing performance; 3) High flexibility to reduce the risk of "kickback".
Spring coil manufacturers often face several challengesduring the production and assembly of the push rod:
● The transition section has a complex structure design, and minor protrusions in the assembly process can cause the thin-walled heat shrink tubing to rupture.
● The thin-walled heat shrink tubing is prone to bending or wrinkling during the assembly process, which increases the difficulty of the operation and reduces production efficiency.
● The transition section has a significant change in diameter, and there is a certain probability that the heat shrink tubing may not conformtightly, necessitating rework and remaking. More problematically, some minor shrinkage issues are difficult to identify, which could lead to defective products reaching hospitals, affecting the operator's experience and even the surgical outcome.
AccuPath® PET heat shrink tube solution
AccuPath® has innovatively developed PET heat shrink tubing technology that offers excellent performance characteristics, , such as ultra-thin walls (0.00015"), high strength (≥20,000 psi), high insulation (4000V/mil), and a high shrink ratio (≥2:1). Moreover, it enhances the resistance to bending or wrinkling under thin-wall conditions, providing the most comprehensive solution for spring coil manufacturers. This advancement enhances the customers' process capabilities and product quality.
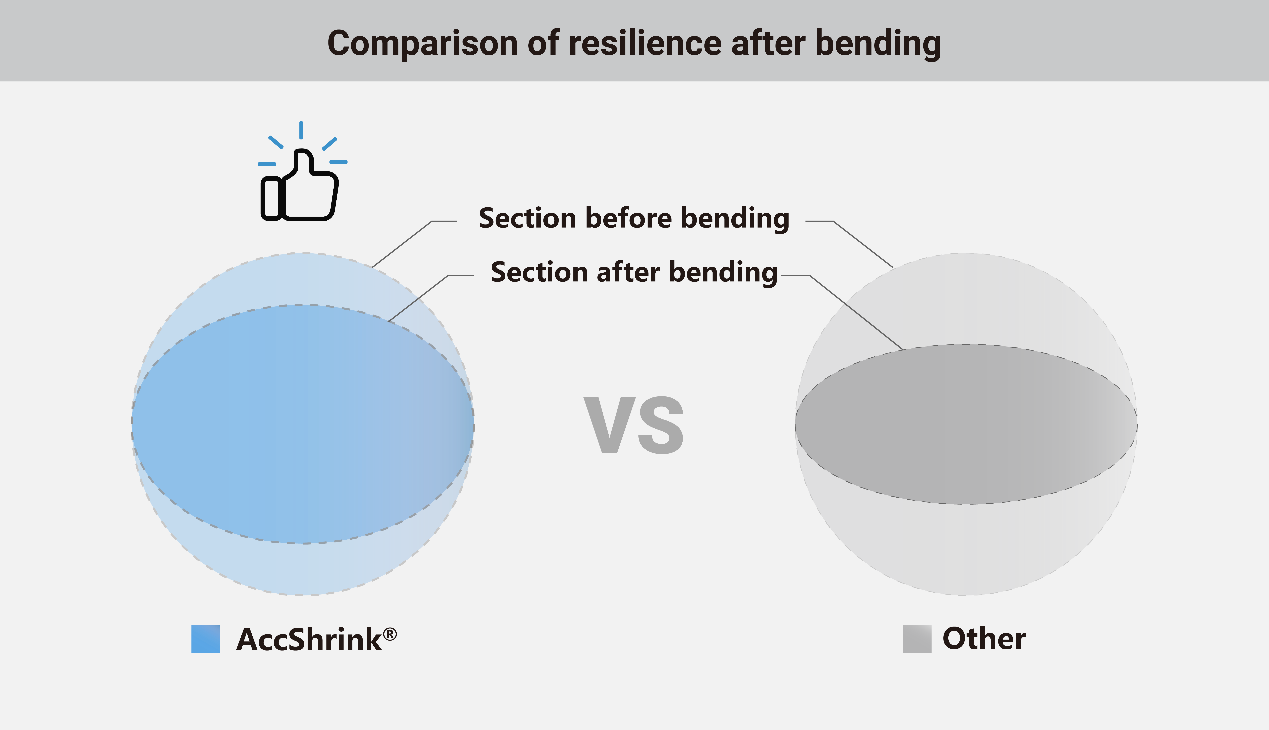
AccShrink® vs. Competitors: Comparison of Resiliency After Compression (AccShrink® rebounds to a near tubular state.)
AccuPath® produces over 300 sizes and specifications of medical PET heat shrink tubing, with product specifications covering an inner diameter range from 0.006 inches to 0.320 inches, a wall thickness range from 0.00015 inches to 0.003 inches, and a heat shrink ratio from 1.15:1 to 3:1, ensuring precise adaptation to different medical products and surgical scenarios.
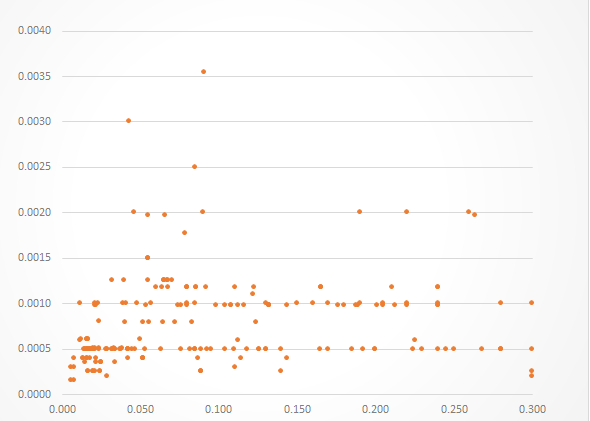
AccShrink® PET Heat Shrink Tubing Specification Matrix
Quality control
In terms of quality management, AccuPath® strictly implements the ISO 13485 quality system standards, regularly evaluates measurement systems to ensure accuracy and reliability, and continuously conducts process capability monitoring and analysis for improvement. The process capability index (Cpk) for PET heat shrink tubing exceeds 1.33, indicating a high level of process performance and fully meeting the standards for key quality characteristics.
Cost control
In terms of cost control, AccuPath® continuously optimizes its processes and introduces automated solutions to improve the pass rate and production efficiency while minimizing production costs, providing customers with more cost-effective PET heat shrink tubing products.
Delivery aspect
Regarding delivery times, AccuPath® can provide samples for standard specifications within 3 days, and for custom specifications within 2 weeks. The delivery time for formal orders is one month.
Post time: May-11-2024