
Abstract:
The application of Ni-ti Tubes in interventional medical devices is becoming increasingly widespread, bringing revolutionary progress to the medical device field with their super elasticity and shape memory characteristics. AccuPath® produces high-standard Ni-ti Tubes through cutting-edge technology and strict quality control. Not only does it lead the industry in dimensional accuracy and performance stability, but it also shows outstanding results in purity and surface treatment technology. These innovative products and customized services will undoubtedly promote safer treatment solutions in the medical device industry.
Integration of Cutting-edge Technology and Exquisite Craftsmanship
During the production process of Ni-ti tubes, AccuPath® selects the appropriate forming process by understanding the metal flow variation among different cold working deformation rates, different annealing states, and various processing methods. This ensures that the tube material flow does not produce local accumulation phenomena. The dimensional accuracy of Ni-ti alloy tubes is controlled from details such as the relationship between strength and toughness, work hardening rate, and wall thickness expansion. In performance adjustment and control, AccuPath® deeply studies the microstructure evolution during the annealing process, grasps the strengthening and toughening mechanism of Ni-ti alloys, and further optimizes mechanical properties to achieve the best strength-ductility match, thus meeting the requirements of various medical device applications.
Strict Quality Management, Creating Industry Quality Benchmarks
The production of AccuPath® Ni-ti tubes includes a series of precise steps, from tube billet preparation to final quality inspection. Piercing, rolling, drawing, annealing, cleaning, and surface treatment, each step is accompanied by strict quality checks to ensure precise control of alloy composition and minimal impurities, thereby ensuring the product's chemical purity and microstructure characteristics.
The company has strict supervision from requirement acquisition to review, production, inspection, and until shipment to ensure product quality. In addition, sample retention during the production process ensures product traceability, laying a solid foundation for quality traceability and continuous improvement. Relevant test data show:
- Microstructure of Raw Materials
The maximum size of porosity and non-metallic inclusion particles in the microstructure of raw materials is optimally controlled within 5.4μm, and the maximum area ratio is only 0.5%.
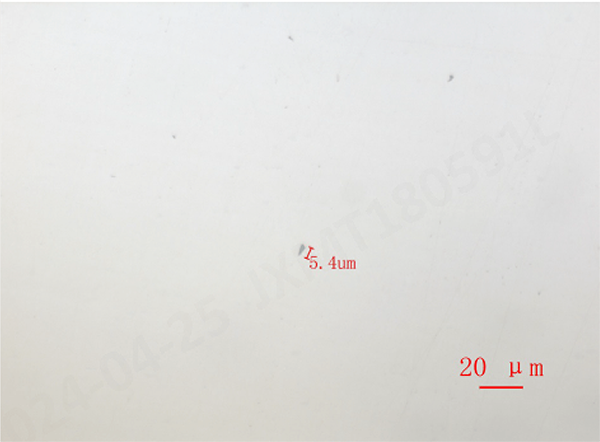
Figure 1: Inclusion in the Sample 500x
Microstructure of Finished Tube Material
The grain size of the finished tube material reaches grade 7, with no obvious pores and inclusions found. The porosity rate and non-metallic inclusion content are extremely low, with an area percentage of only 0.2%.

Figure 2: Grain Size of the Sample 100x
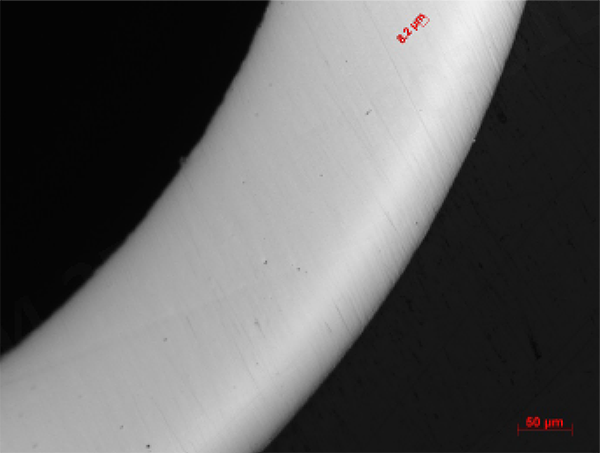
Figure 3: Inclusion in the Sample 200x
Outstanding Mechanical Stability
After meticulous thermomechanical treatment and precise phase transition temperature control, the sample shows outstanding mechanical stability after 20 cycles of 6% strain recovery testing. In addition, the product has excellent adaptability and can be adjusted according to customer needs.
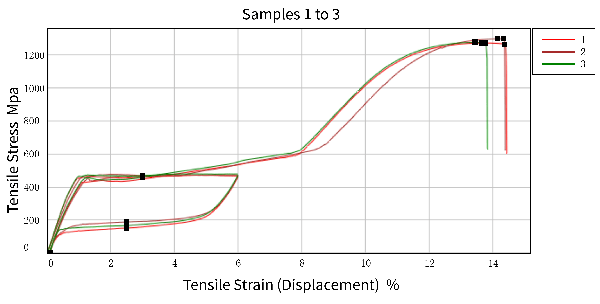
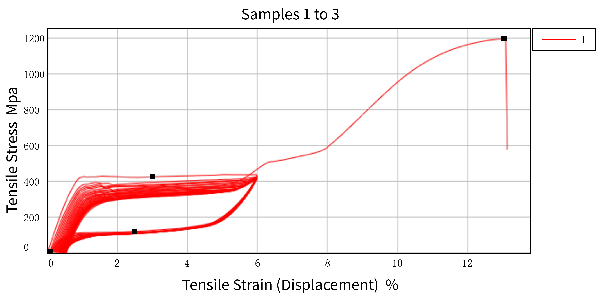
Furthermore, AccuPath® has a complete set of testing equipment and methods that can conduct comprehensive tensile performance tests, thermal expansion analysis, shape memory characteristic determination, fatigue crack propagation, and fracture toughness behavior assessment.
"High Precision, Low Impurity" Ultra-Pure Ni-ti Tubes
With a high-standard quality management system, AccuPath® has developed a series of "high precision, low impurity" innovative ultra-pure Ni-ti tube products. Through testing characterization, the maximum internal impurity size of the product is ≤12.0μm, and the area ratio is ≤0.5%. Using precise extrusion or drawing processes, the 360-degree wall thickness tolerance of the product can be controlled within 0.01mm.
Simultaneously, with the aid of high-precision surface modification techniques such as magnetic grinding and centerless grinding, the roughness (Ra) of AccuPath® Ni-ti tubes reaches ≤0.1μm, effectively enhancing their corrosion resistance and biocompatibility.
Available Size Specifications
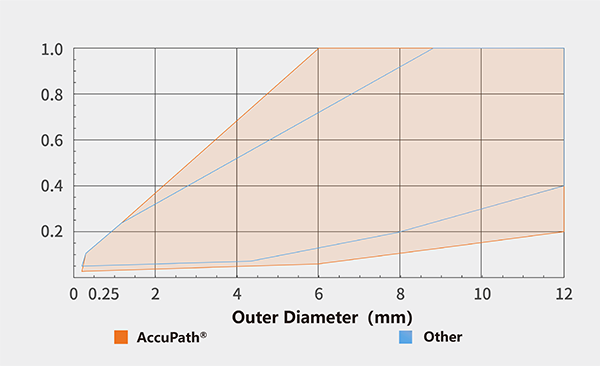
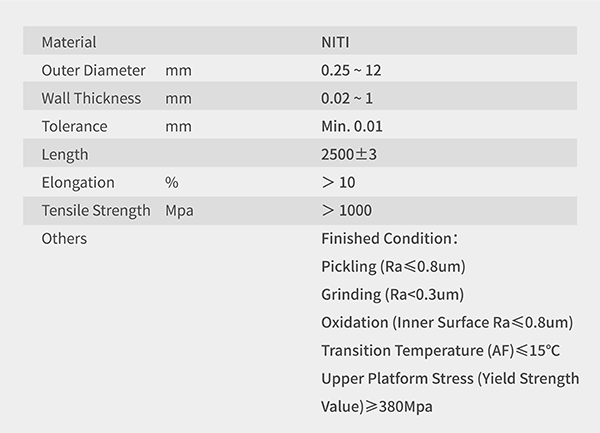
In addition, AccuPath® can also provide customized Ni-ti part processing services according to customer needs, including: laser cutting, thermal shaping, Ni-ti part polishing, etc.
- Laser Welding: The minimum spot diameter can reach 0.003"
- Laser Cutting: The minimum cutting seam width is 0.001" & Maximum repeatability can reach ±0.0001"
- Electrochemical Polishing: Roughness (Ra) ≤0.1μm
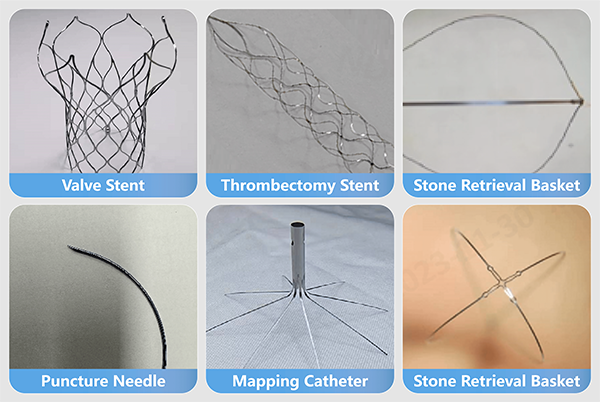
Post time: May-31-2024